Minibytes by Al Allen
Unfortunately, some people still consider the use of chemical dispersants and the controlled burning of oil as “alternative” oil spill response options. Decades of research, controlled field trials and experience during actual oil spills have proven that the application of chemical dispersants and the use of controlled burning can easily match and often exceed the results of physical containment and the recovery of oil with skimmers. The literature is filled with the results of these projects and spill response efforts to the extent that I could never adequately address the depth and significance of these findings in a brief blog. However, as in my previous blogs, I can attempt to give an overview of some of the most important goals and tactics for a given response technique, address the applicability of that technique for different environmental conditions, and provide an assessment of the most important tradeoffs. I am fortunate to have had the opportunity to work throughout my career on each of the three major response options (mechanical recovery, dispersants and burning), and I continue to be convinced that not one of these options can be considered the best, or that others are “alternatives”! There are times, of course, when one or two of these response modes may provide clear advantages for the conditions at hand.
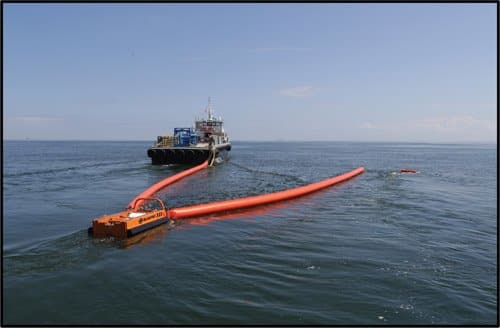
Since a picture is worth a lot of words, Photos 1, 2 and 3 should help fix an image, at least for now, of each response option in at least one of the many ways it could be used. Oil can be skimmed from water with hand tools, buckets, and suction hoses; with rotating drums, belts, mops, and discs; and with various combinations of these and other devices (Photo 1). Oil skimmers may be attached to, or built within, every conceivable size and type of vessel, with single- or multiple-hulls, and from small skiffs to large tanker-class vessels. The choices obviously involve cost, maneuverability, draft, storage capacity, and the key oil-access and removal parameters (from my previous blogs) involving: speed, swath, and throughput/recovery efficiency. And, yes, there is still the need to transit, offload, and dispose of recovered fluids; and to eventually, clean or dispose of every oiled surface (hulls, decks, equipment, protective clothing, hoses, booms, etc.). While slow in covering large areas and relatively expensive, the mechanical recovery of oil does provide a proven, widely accepted and versatile option for a broad range of oil types and conditions at sea, nearshore, in rivers, wetlands, etc. And most importantly, physical removal does not require authorization for its use.
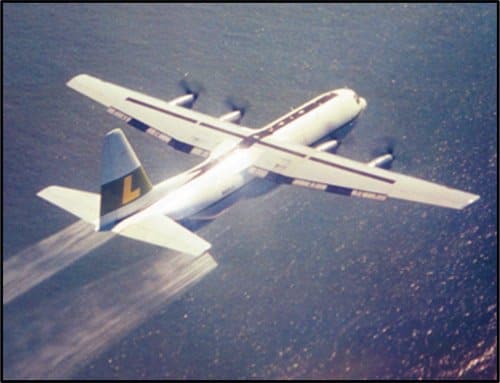
Photo 2 – Hmmm, at first glance this looks a lot easier, working from a large, fast aircraft applying chemical dispersants with the push of a button; sitting in a clean, comfy space out of the weather; and avoiding contact with rough seas and sticky, smelly oil. This option might involve a relatively quick release of the aircraft’s dispersant payload, then offering time to complete some paper work and grab a snack while heading back to base for a rest stop, coffee and another load of dispersant – sure seems “user friendly”. In addition, there is the outstanding high transit speed to get on location and the outstanding oil encounter rate involving high application speeds and broad swathes with aircraft. These performance factors allow for large areal coverage rates (i.e., area covered per minute) that are about 10 to 100 times greater than the coverage rates commonly swept by boats. Recall that most vessel-mounted skimming systems operate at only a knot or two, and that boats spraying dispersants typically work at about 3 to 5 knots.
Another plus with dispersants is that under good conditions with relatively fresh thick oil, dispersant application efficiencies can reach 75% to 95%. And, because dispersants work best with agitation or mixing energy once applied, the higher wind and wave conditions often encountered on open water are preferred. Such wind and sea states, while fine for dispersant use, may reach a condition where conventional booms and fire-resistant booms may lose their effectiveness in capturing and holding oil for recovery or burning. Such is the case for booms operating in short-period (choppy), wind-driven waves about 3 to 5 feet in height where white-caps begin to form.
It should be clear that dispersants don’t “cleanup” or “remove” oil from the sea, and they don’t “sink” oil. They simply modify certain physical and chemical properties of the oil treated, allowing the oil to break into extremely small droplets that can mix into and dilute within near-surface waters. Such tiny oil droplets, mere fractions of a millimeter in diameter, are then subject to significantly accelerated natural dispersion and degradation processes within the water column. Oil concentrations will often drop below toxicity levels of concern within hours. However, in order to minimize any harmful impacts, considerable attention is given to the potential for a brief exposure of marine biota to elevated hydrocarbon levels, and to appropriate water depths to prevent contact with benthic (bottom-dwelling) communities.
Some of the operational considerations for dispersant use (just like most oil slicks) really need to be viewed from a higher perspective at times, remembering that the oil to be treated must be visible, of sufficient condition and thickness, and spatially distributed so that dispersant can be applied effectively to the oil. Dispersants are expensive, and should be applied accurately to justify their use. Flying at relatively low altitudes of about 100 to 150 feet or less (depending upon aircraft type, visibility, wind/sea conditions, etc.), pilots and operators of a system almost always need good “spotter” support. That is, an additional aircraft is needed with well-trained observers aboard to position the application aircraft over dark (thick) oil slicks, while working to achieve a proper approach, the turning on and off of dispersant pumps, and an allowance for dispersant drift off target due to wind. All spill response personnel know just how variable the size, shape and thickness of slicks can be, making it very difficult to put the dispersant on the oil at a high speed, while minimizing any waste of dispersant on water only or on slicks too thin to justify dispersant use. There are still other precautions involving dispersants including the staging of adequate inventories of dispersant to meet emergency needs; the proper storage, maintenance and testing of the chemical over long periods; and the creation of a sound backup plan for the supply and transport of potentially large volumes of dispersant to support a long-term, major event.
A final and most important constraint involving the application of dispersants is the requirement for permission to use them. A request for authorization to use dispersant should not start at the time of a spill. A timely approval for dispersant use will depend upon the proposed location for use (distance offshore, water depth, potentially exposed biota, etc.); federal, state and local regulations; and knowledge/attitudes in the community about the net benefits, potential impacts, and tradeoffs regarding dispersants and other options available. Because of these and other complicated issues that can stop or slow down a request for dispersant use, it is essential that response organizations plan ahead to streamline the dispersant authorization process, and to work closely with regulators, the public and the press involving the pros and cons of dispersant use. For most offshore response organizations, it is important to acquire and maintain dispersant application systems, adequate dispersant stockpiles, and trained response personnel. The application of dispersants, especially from large fixed-wing aircraft, is an efficient method, under the right conditions, for the treatment of large quantities of spilled oil, and a significant reduction of harmful impacts to waterfowl and other marine plants and animals.
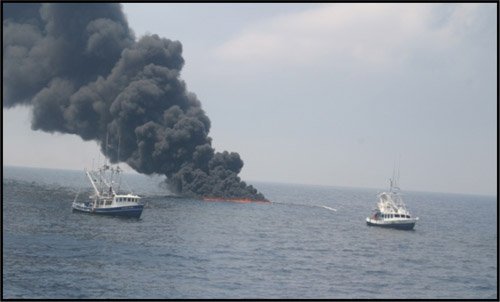
Well…, I’ve reached the acceptable limit of “Blog-Length” if I am to stick with my goal (and with my blog title) of “Minibytes by Al Allen”! Therefore, I seek your patience in completing my brief overview of response option comparisons & tradeoffs. I will leave Photo 3 in this blog to ignite your imagination for the next blog (#6) where some very HOT topics will be addressed!
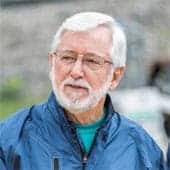
Alan A. Allen has over five decades of experience as a technical advisor and field supervisor involving hundreds of oil spills around the world. Al is recognized as a leading consultant and trainer involving oil spill surveillance and spotting techniques, the application of chemical dispersants, and the containment, recovery and/or combustion of spilled oil under arctic and sub-arctic conditions.
Copyright© 2018, Al Allen. Unauthorized use and/or duplication of this material without express and written permission from this blog’s author is prohibited.